
For other hydraulic and pneumatic two in one experimental benches, please click on the left!
YQ-C Industrial Hydraulic and Pneumatic (2-in-1) Comprehensive Experimental Platform
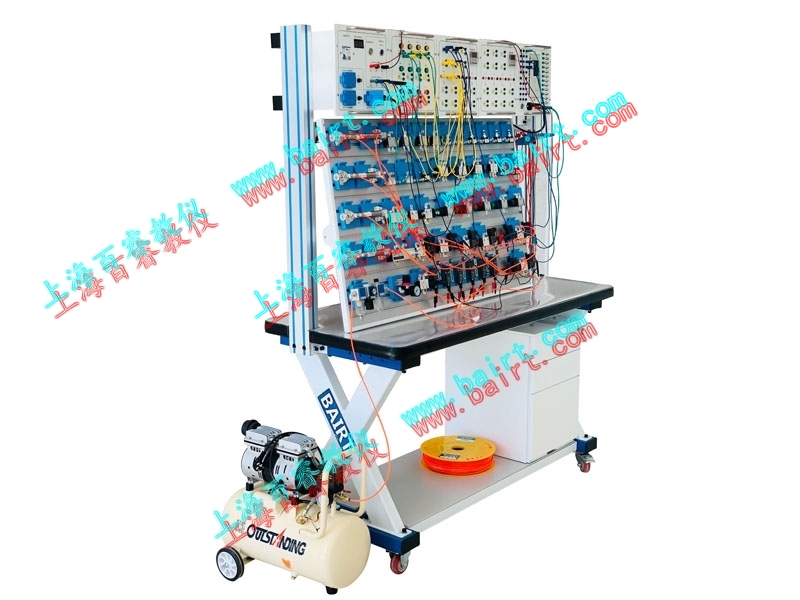
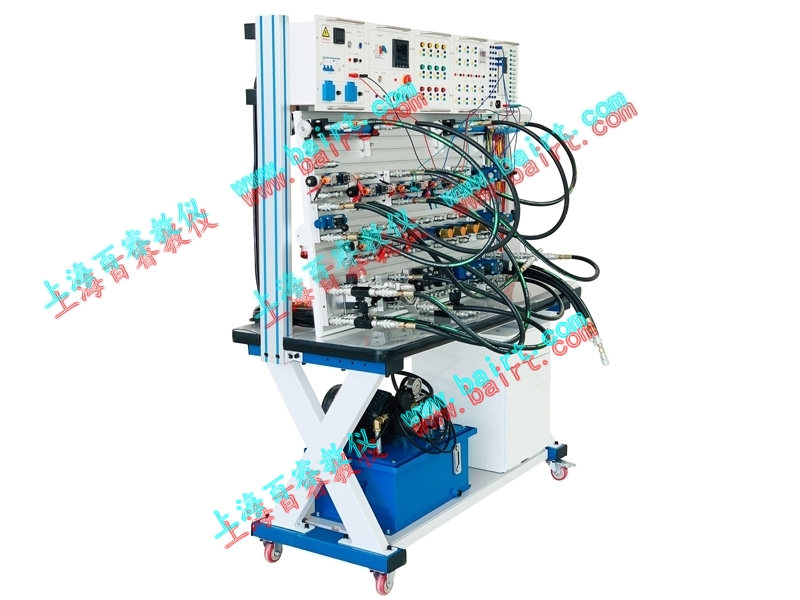
Fashionable profile design

Regular style
The YQ-C industrial hydraulic and pneumatic comprehensive experimental platform is designed based on modern teaching characteristics and the latest requirements of the hydraulic transmission curriculum teaching outline. It adopts advanced Rexroth technology hydraulic components and unique modularity, forming a convenient system combination that meets the experimental teaching requirements of hydraulic transmission tutorials for students in higher education institutions, secondary professional schools, and vocational and technical schools; The goal is to cultivate students' hands-on, design, and comprehensive application abilities, and to enhance and strengthen their innovative design abilities.
Hydraulic surface:
1、 Main features:
1. The system adopts standard industrial hydraulic components, which are safe and reliable to use and close to industrialization.
2. Fast and reliable connection method, special sealing interface, ensuring convenient and fast experimental assembly, no oil leakage during disassembly, and clean.
3. Accurate measuring instruments, convenient measurement methods, simple to use, and precise and reliable measurements.
4. Using programmable logic controllers (PLCs) to communicate with microcomputers, achieving electrical automation control, online programmable monitoring, and fault detection.
① Performance testing of commonly used hydraulic components
1. Characteristic testing of hydraulic pumps
2. Characteristic testing of relief valve (static testing)
3. Characteristic testing of throttle speed control valve
② Hydraulic transmission basic circuit experiment:
Relief valve pressure regulating circuit simple pressure regulating circuit
Relief valve buffer circuit secondary pressure circuit
A pressure regulating circuit for multiple relief valves in a bidirectional pressure adjustment circuit
The pressure reducing circuit of the pressure reducing valve and the unloading circuit of the directional valve
Unloading circuit of pilot operated relief valve, balancing circuit of sequence valve
Speed regulation circuit speed control valve short circuited speed switching circuit
Throttling valve inlet oil throttling speed control circuit Throttling valve return oil throttling speed control circuit
Speed control valve inlet oil throttle speed control circuit Speed control valve return oil throttle speed control circuit
Throttling valve, variable pressure throttle speed control circuit, speed control valve, variable pressure throttle speed control circuit
Oil inlet throttle speed control circuit, oil return throttle speed control circuit
Directional control circuit pressure holding (self-locking) circuit
Dual cylinder working control circuit sequence valve sequence action circuit
Electrical stroke switch sequential action circuit, pressure relay sequential action circuit
Practical training on using PLC to control hydraulic circuits and system hydraulic transmission performance
③ Students can design and assemble up to 80 types of extended hydraulic circuit experiments on their own
④ Programmable Logic Controller (PLC) electrical control experiment, in the form of mechatronic and hydraulic integrated control experiment.
1. Learning PLC instruction programming and ladder diagram programming
2. Learning and Using PLC Programming Software
3. Communication between PLC and computer, online debugging and monitoring
4. Optimization of PLC for Hydraulic Transmission Control
5. Equipped with a loader simulation mechanism.
1) Observing the structure of various components in hydraulic transmission and studying and analyzing the principles of hydraulic control systems.
2) Hydraulic loading machinery demonstration control experiment.
① Loading operation, after the bucket is loaded, the rocker arm cylinder extends to reverse the bucket and lift the boom;
② Unloading operation, bucket unloading (rocker arm retracted, causing bucket to turn), boom lowering.
Pneumatic surface:
Main features:
1. Modular structural design and experimental setup are simple and convenient, with each pneumatic component forming an independent module and equipped with a convenient installation base plate. During the experiment, various experimental circuits can be freely assembled on a universal aluminum alloy profile plate, and the operation is simple and fast.
2. Quick and reliable connection joints, easy and time-saving disassembly.
3. Adopting standard industrial pneumatic components for reliable and safe performance.
4. A low-noise working pump station provides a quiet experimental environment (noise<60).
Experimental project:
① PLC control circuit experiment:
1. Reversing circuit of single acting cylinder 2. Reversing circuit of double acting cylinder
3. Primary pressure control circuit 4. Secondary pressure control circuit
5. High and low pressure switching circuit 6. Double acting cylinder bidirectional speed regulation circuit (inlet regulation, outlet regulation)
7. Speed switching circuit 8. Buffer circuit
9. Interlocking circuit 10. Overload protection circuit
11. Position controlled single reciprocating circuit 12. Pressure controlled single reciprocating circuit
13. Time controlled single reciprocating circuit 14. Single double acting cylinder continuous reciprocating action circuit
15. Synchronous circuit using throttle valve 16. Three cylinder linkage circuit
17. Counting circuit 18. Delay circuit
19. Application circuit (or logic) of logic valve 20. Two handed operation circuit
② Relay control circuit
Cylinder buffer circuit, cylinder feed system, dual cylinder action circuit
③ Programmable Logic Controller (PLC) Electrical Control Experiment, Mechatronics Electric Gas Integrated Control Experiment:
(1) Learning PLC instruction programming and ladder diagram programming
⑵ Learning and using PLC programming software
⑶ Communication and online debugging between PLC and computer
Control experiment combining PLC and pneumatic
PLC instruction programming training
④ Students design, assemble, and expand various circuit experiments on their own
Composition of the experimental platform:
① Experimental workbench (shared by hydraulic and pneumatic systems)
The experimental workbench is composed of an iron body and an aluminum alloy panel (T-shaped hook groove), etc.
Workbench size: long × wide × Height=1600mm × 700mm × 1850mm (with a packaging weight of approximately 300kg)
② Hydraulic pump station
Rated working pressure of the system: 6.3Mpa. (Up to 7Mpa maximum)
⑴ Motor pump device (1 unit)
Variable vane pump -1 motor: unidirectional, nominal displacement 6.67mL/r, volumetric efficiency 90%;
Motor: three-phase AC voltage, power 2HP 4P, speed 1450r/min;
⑵ Fuel tank: nominal volume 45L; Equipped with liquid level and oil temperature indicators, oil suction and return filters, safety valves, etc
Pneumatic pump station:
Air pump input voltage: AC 220V/50Hz Motor (dual head) Power: 250W
Rated output pressure: 0.8Mpa Air pump volume: 20L
Working noise:<60 decibels
③ Common hydraulic components
The main components are Bosch Rexroth technology components, and the configuration is detailed in the configuration list.
Each hydraulic component is equipped with an oil transition bottom plate, which allows for easy and flexible placement of hydraulic components on aluminum alloy panels.
Pneumatic components:
Mainly using JELPC (Jiaerling) pneumatic components, please refer to the list for configuration details.
All pneumatic components are equipped with aluminum alloy transition base plates (engineering plastics), which can be conveniently and freely placed on the experimental panel (aluminum alloy profile structure with "T" grooves on the panel). The circuit overlap adopts a quick change joint, which is convenient and fast for disassembly and connection.
④ Electrical measurement and control unit
Double sided: Programmable Logic Controller (PLC): Siemens S7-200 series, I/O port 24 points, relay output form, power supply voltage: AC 220V/50Hz, control voltage is DC24V, with manual, automatic, sequential and other control functions
The experimental platform consists of several parts, including an experimental stand, a working pump station, pneumatic components, and an electrical control unit.
Jiangsu Bairui Education Equipment Co., Ltd. is a production, research and development sales base established and constructed by Shanghai Bairui Education Equipment Group in Suqian City, Jiangsu Province in December 2016. According to the group's requirements, it aims for practical training and is a technology-based enterprise that integrates professional research and development, manufacturing, and sales. Dedicated to the production and sales of specialized products in the fields of intelligent flexible automation, robot cooperation, hydraulic and pneumatic, mold design and manufacturing, mechanical innovation design, and mechanical processing manufacturing in the mechanical majors of undergraduate, vocational, and technician colleges in higher education institutions. Bairui Education Instrument, an enterprise that has obtained national high-tech certification, is located in the dynamic Yangtze River Delta, relying on the Shanghai R&D center. Its production and sales factory is located in Suqian City, Jiangsu Province. It has favorable conditions such as a good investment and financing environment, strong scientific research capabilities, advanced manufacturing technology, strong manufacturing capabilities, convenient transportation, and beautiful ecology. The company covers an area of over 30000 square meters in production and office, with advanced complete processing equipment and complete product testing processes. The company has set up R&D Technology Department, Marketing Department, Work Safety Department, Finance Department, Logistics Supply Department and science and technology research team. The humanized management system is perfect, the supervision mechanism is perfect, and the ISO9001:2015 international quality management system has been operating in a standardized and strict manner for many years. The company has passed the OHSAS18001:2007 occupational health and safety management system certification, ISO14001:2015 environmental management system certification, and passed the GB/T29490-2013 intellectual property management system certification in 2020. It has been rated as: excellent supplier of government procurement, China's independent innovation brand, China's key recommended enterprise in the teaching equipment industry, excellent enterprise in the teaching equipment industry in China, national energy-saving and environmental protection products, and exemplary organization of after-sales service in the education equipment industry for many consecutive years; Obtained AAA level demonstration unit for honest operation, AAA level contract abiding and trustworthy enterprise, AAA level credit rating enterprise, AAA level credit enterprise, National 315 Integrity Enterprise, Top 100 Enterprises in the Industry, National Quality Trustworthy Product, and National Authoritative Testing Quality Qualified Product Certificate. The research team of Jiangsu Bairui Education Instrument has been committed to product improvement and innovation for a long time. They have developed nine series of nearly a hundred stable and advanced science and engineering teaching and training experimental equipment, making our company's basic practical and innovative technology products have a clear advantage in peer competition!